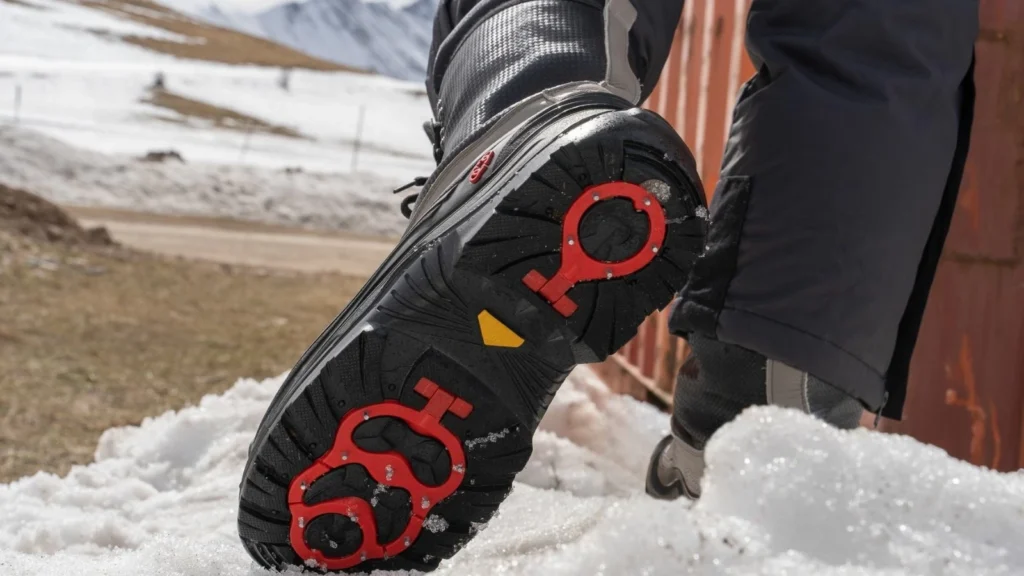
All’interno di questo articolo ti parlerò delle più importanti caratteristiche e differenze dei materiali utilizzabili per la produzione di suole per le calzature al fine di offrire una panoramica esaustiva sull’argomento.
Abbiamo fatto molta strada rispetto ai primi materiali utilizzati per i fondi delle nostre calzature, all’inizio gli elementi naturali come il legno e il cuoio facevano da padroni e poi gradualmente ci siamo indirizzati verso il mondo del sintetico, arrivando ai primi esperimenti di vecchi copertoni che, utilizzati come gomme, hanno agito da prototipi di quello che poi avremmo sviluppato nel tempo.
Il mercato della moda e delle calzature è da sempre improntato ad un miglioramento costante legato alla modifica delle esigenze del pubblico, e questo ci ha dato la possibilità di procedere verso un processo evolutivo delle differenti tipologie di materiali.
Ciò nonostante non è affatto facile comprendere le reali caratteristiche, le differenze nonché le similitudini di questi componenti, ed il nostro intento in questo articolo è proprio cercare di fare un po’ di chiarezza a riguardo.
I tre elementi principali da prendere in considerazione quando parliamo di materiali plastici sono:
- caratteristiche tecniche;
- lavorabilità e stampabilità;
- elementi di carattere estetico.
Ma andiamo più nel dettaglio.
Per comodità, è utile effettuare una differenziazione tra due diverse categorie:
A. Materiali termoplastici;
B. Materiali reticolati/vulcanizzati.
La categoria A fa riferimento alla famiglia dei cosiddetti termoplastici, significa sostanzialmente che quando ci affidiamo a questi componenti, tramite l’ausilio della temperatura riusciamo a mantenere un materiale plastico e successivamente, attraverso il processo di compressione ottenere la forma desiderata. A questa famiglia, appartengono il TPU, il TR ed il PVC, etc..
Il TPU è un poliuretano caratterizzato da una catena polimera, una catena aperta in base alla quale un manufatto può essere sminuzzato e reinserito all’interno del processo produttivo. Questo materiale prevede un procedimento di realizzazione nettamente più ecologico rispetto ad altri componenti, in quanto il materiale di scarto può essere recuperato.
Subito dopo troviamo il TR, una gomma termoplastica senza vulcanizzanti, leggera e riciclabile ed infine il PVC o polivinilcloruro, un componente la cui materia prima ha un prezzo molto basso e permette un’ottima lavorabilità.
La categoria B riguarda invece quei materiali modellabili come la Gomma, l’EVA e il PU, tre elementi che solitamente si definiscono vulcanizzati o reticolati, e con questo intendiamo dire che nel processo produttivo ci troviamo di fronte ad una catena chiusa, che diventa stabile e non può più essere scissa.
Il processo di reticolazione della Gomma e dell’EVA, si verifica tramite un effetto chimico ed uno legato a fattori quali temperatura e pressione, nel caso del PU invece, temperatura e pressione non subentrano in modo così significativo.
Insomma fin qui risulta piuttosto evidente che la temperatura sia il fattore principale che va ad influenzare le caratteristiche tecniche di un prodotto, ed essa può dipendere da proprietà ambientali o dalla cosiddetta termo-abrasione, derivante dall’attrito e quindi dall’usura di un prodotto.
All’aumento della temperatura corrisponde una diminuzione dell’abrasione e questo porta inevitabilmente ad una diminuzione di quelle che definiamo caratteristiche tecniche.
Riassumendo, in relazione alle caratteristiche fisico – meccaniche, la categoria B dei cosiddetti materiali reticolati ci fornisce delle caratteristiche tecniche stabili nel tempo, mentre la categoria A delle caratteristiche tecniche instabili.
Un ulteriore elemento che nel settore calzaturiero ricopre un ruolo fondamentale oltre alla tenacità e all’abrasione è il peso specifico o la cosiddetta leggerezza. Ciò significa che tutti i suddetti materiali hanno un peso diverso e per un decimetro cubo, quindi un litro di materiale, uno stesso stampo può avere un peso specifico molto differente:
- Gomma: 1,2kg circa
- TR 0,92/1,02kg
- TPU: 1,18/1,20kg
- PVC 1,18/1,22kg
- PU 0.65kg
- EVA, la leggerezza per antonomasia, il peso varia in funzione dell’espansione, ed il rapporto di peso può variare da 0,24 a 0,75.
Il secondo fattore che va preso in considerazione, a seguito delle caratteristiche tecniche è la stampabilità o lavorabilità.
Il numero di lavorazioni che devono essere effettuate difatti, influisce su un aspetto fondamentale e cioè il prezzo. Un materiale come la gomma ad esempio, prevede un costo della materia prima non particolarmente elevato, tuttavia il numero di lavorazioni necessarie per la trasformazione a prodotto finito è piuttosto significativo, contrariamente ad un materiale come l’EVA, il cui prezzo della materia prima tende ad essere maggiore, ma il numero di lavorazioni è decisamente inferiore.
Il prezzo viene quindi definito sulla base del costo dalla materia prima ed il numero di trasformazioni.
L’ultimo fattore che bisogna analizzare prima di decidere verso quale materiale indirizzarsi è sicuramente l’elemento estetico, in quanto ovviamente acquisendo caratteristiche tecniche migliori, tendiamo a perdere elementi legati all’estetica del prodotto finale e viceversa.
Personalmente in AL.PI con il sistema di suole brevettato Ocsystem cerchiamo di trovare un giusto compromesso tra durabilità ed estetica, mentre per la realizzazione di un prodotto ad uso quotidiano si può prediligere la nostra Commodo, progettata per rendersi estensibile in larghezza al fine di facilitarne la calzata ed il comfort.
E’ insomma necessario, come sempre, trovare il giusto equilibrio al fine di compiere la scelta che risponda al meglio alle nostre esigenze.
E se dovessi avere ancora dei dubbi, non esitare a contattarci per una consulenza o semplicemente per avere il nostro supporto nella scelta del materiale migliore per la realizzazione delle tue suole.